In electrical equipment such as motors and transformers, laminated steel core is a key component to improve energy efficiency and reduce energy loss. Its design helps suppress eddy currents generated inside the motor, thereby reducing heat generation and losses. The ingenuity of this structure makes it an indispensable component in electrical equipment.
1. What is laminated steel core?
Laminated steel cores are typically constructed from a series of thin layers of silicon steel laminated on top of each other, with insulating material separating each layer. Compared with the design of solid steel blocks, this laminated structure can significantly reduce the formation of internal eddy currents, making the motor run more efficiently [[1](https://www.powerservicesgroup.com/2016/01/why-is- a -stator-core-made-of-laminated-steel/)].
2. Principle of stacked design
When a motor or transformer is operating, the internal magnetic field induces eddy currents in the core material. Eddy currents generate heat and cause wasted energy. By layering the core materials and adding insulators between the layers, the path of the eddy currents is blocked, thereby reducing heat generation and energy loss in the core. The laminated design therefore allows the motor to operate more efficiently and also extends the service life of the equipment [[1](https://www.powerservicesgroup.com/2016/01/why-is-a-stator-core-made-of-laminated -steel/)].
3. Application of laminated steel core
Laminated steel cores are widely used in motors, generators, transformers and other equipment. Especially in high-power and high-frequency operating environments, its energy efficiency improvement is particularly obvious. In the power industry, equipment using laminated steel cores can reduce losses and increase output power, and is an effective means to improve the overall performance of the equipment.
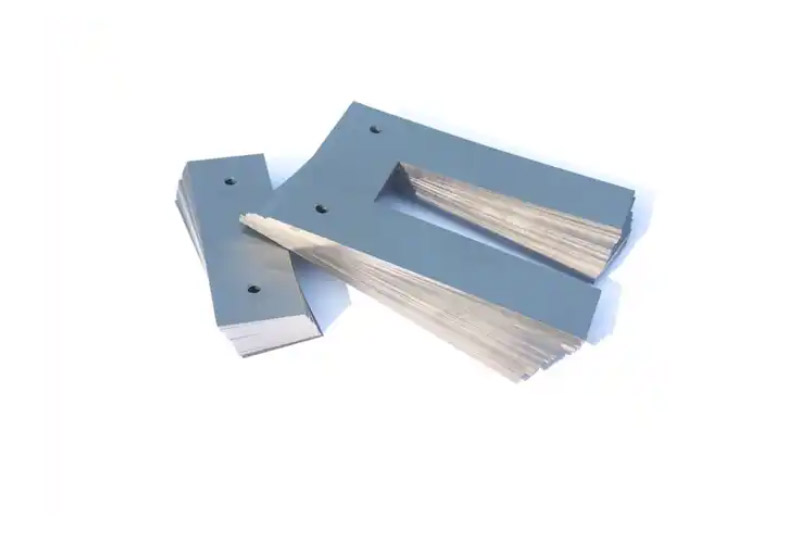